1. Creativity and Experience in Handling Diverse Precision Sheet Metal Processing Daily
Being a prototype sheet metal manufacturer means encountering “new jobs every day,” often dozens of them. While investing in the latest machinery is essential, the ability to think quickly and effectively on the shop floor greatly influences quality, especially given the premise that no two orders are ever the same
- Designing optimal processes during estimation
- Referring to past project databases to predict outcomes
- Sharing deadlines in real-time to ensure collective responsibility
What is the capability to handle one-off prototypes?
Accurately bending complex shapes or drilling multiple precise holes requires extensive knowledge and years of experience in precision sheet metal processing. The procedures and methods used by skilled technicians are digitized and referenced when processing similar shapes. Likewise, when internal defects occur, we conduct thorough process reviews, implementing corrections that contribute to future improvements.
At our company, we don’t limit ourselves to sheet metal equipment alone for processing. By combining techniques like wire cutting and machining, we can produce prototypes and one-off items more efficiently. For example, when dealing with a design that requires multiple precision holes near deep-drawn shapes, we achieve high accuracy by performing hole drilling after pressing and cutting the outer perimeter using wire cutting.
2. Over 300 Bending Dies in Stock
In precision sheet metal processing, machines called press brakes (or benders) are used to bend metals such as stainless steel and aluminum. A punch die is mounted on the upper part of the machine, while a die mold is attached to the lower part. The machine applies mechanical pressure to form flat sheets into the desired shapes.
Bending processes always require specific molds. Our company owns a wide variety of dies, including those for deep bending and radius (R) bending, enabling us to handle diverse bending requirements.
- Over 30 years’ worth of bending molds accumulated since our founding
- Specialized dies for deep bending and other unique processes
- A wide range of sizes available
These resources allow us to achieve fast and precise sheet metal processing.
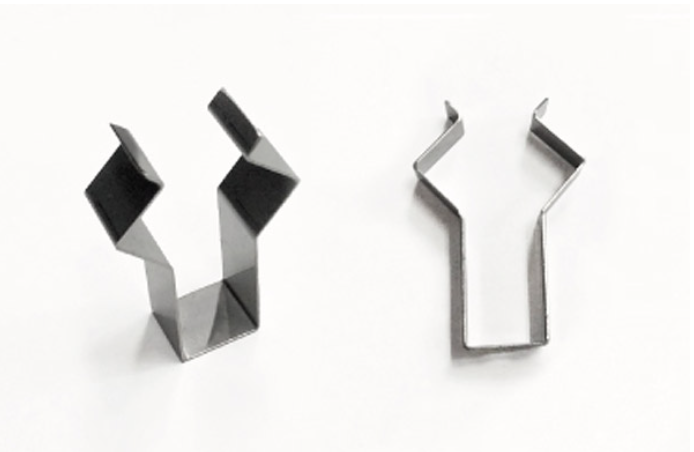
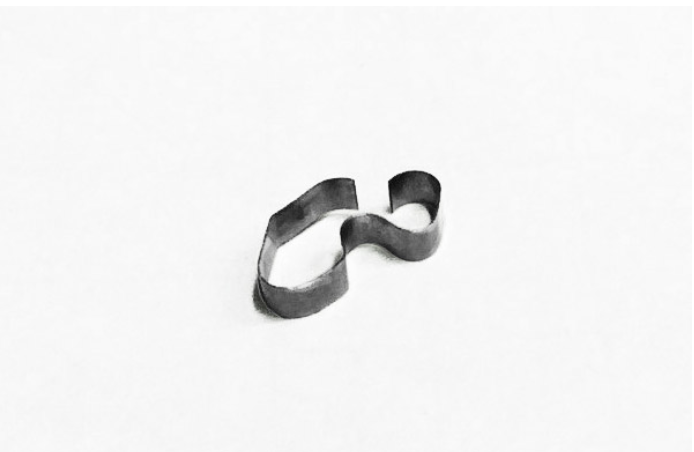
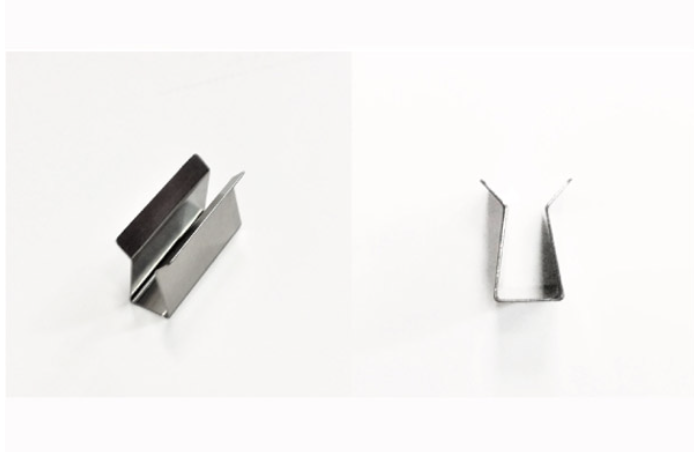
3. Complex Drawing Processing Without Metal Dies
In sheet metal drawing, pressure is applied to a single metal sheet using a die to create concave and convex shapes.
Metals possess a property called plasticity, which means that once deformed beyond a certain point, they do not return to their original shape. Drawing utilizes this property to form complex, contoured shapes from a single sheet without the need to weld multiple parts. For prototype drawing processes, we employ die-less methods using stacked molds.
- Achieves complex shapes without welding
- Enables drawing processes without creating full-scale dies
- Reduces the number of production steps
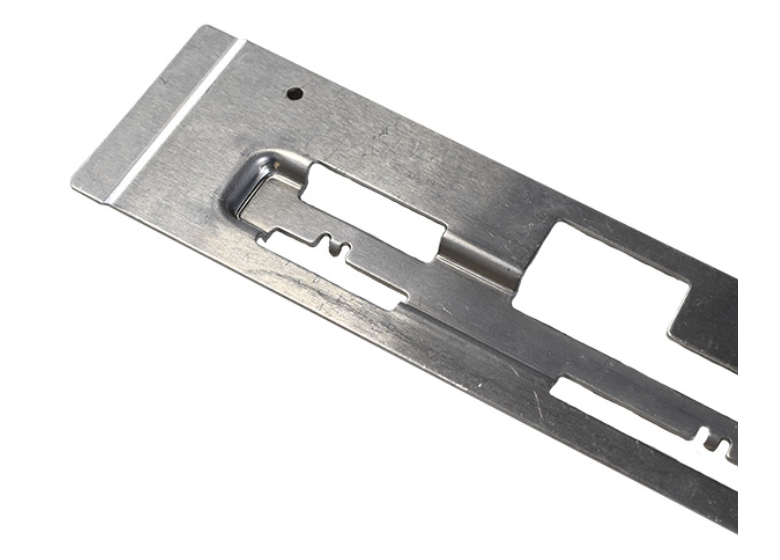
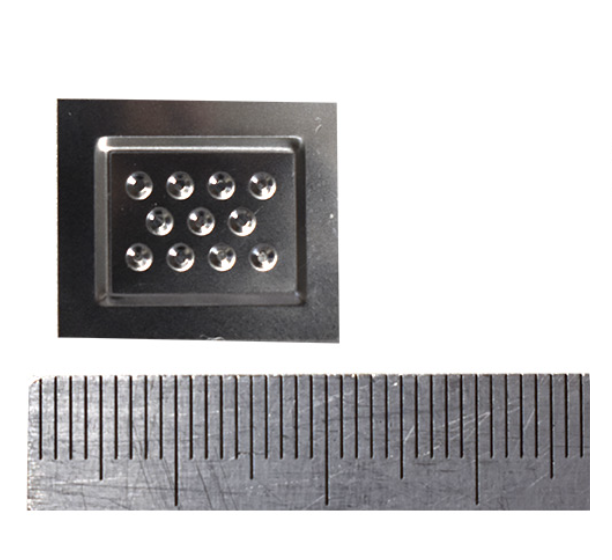
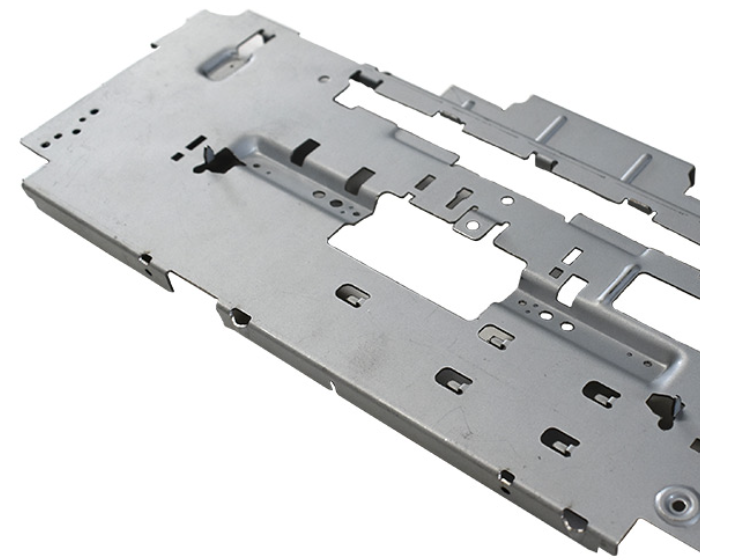
4. Extensive Stock of Sheet Metal Materials
We maintain an extensive inventory of materials to meet short lead times, including steel sheets, galvanized steel, stainless steel, spring materials, aluminum, copper, brass, and phosphor bronze. Specialized materials such as SUS316 surgical-grade stainless steel for medical use and embossed materials for food-related applications are also kept in stock.
- Steel [SPCC]: 0.4mm–9.0mm / [SECC (galvanized steel)]: 0.4mm–3.2mm
- Stainless Steel [SUS]: 0.01mm–6.0mm (grades 301, 304, 316, 430, etc.)
- Aluminum [A5052]: 0.3mm–6.0mm
- Brass & Copper: 0.01mm–400mm
We stock diverse materials suitable for applications such as inspection equipment, measuring devices, industrial printers, semiconductors, electronics, automotive, medical, food, apparel, and store fixtures. For other materials, feel free to consult us.
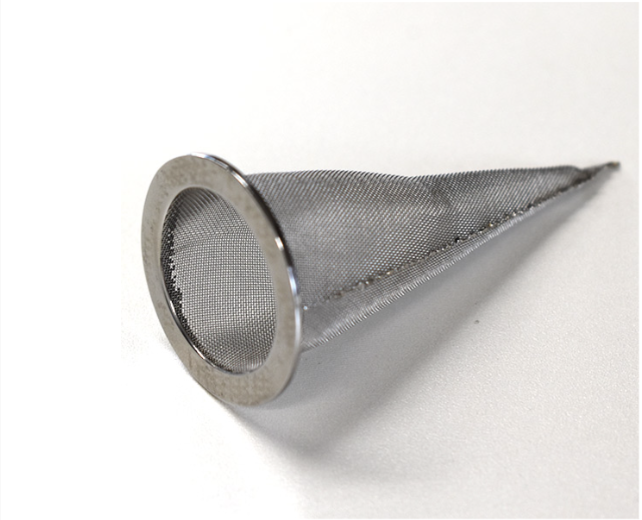
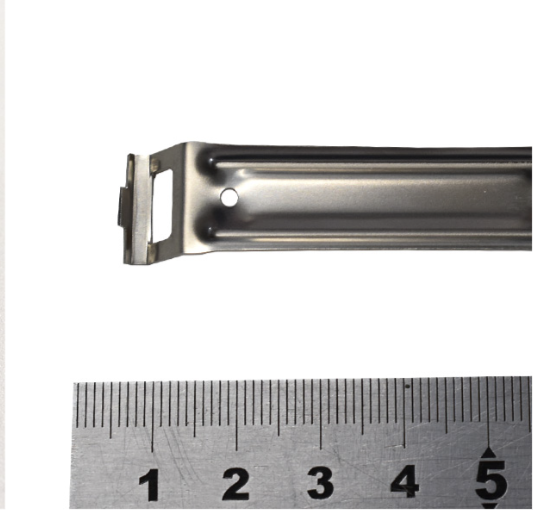
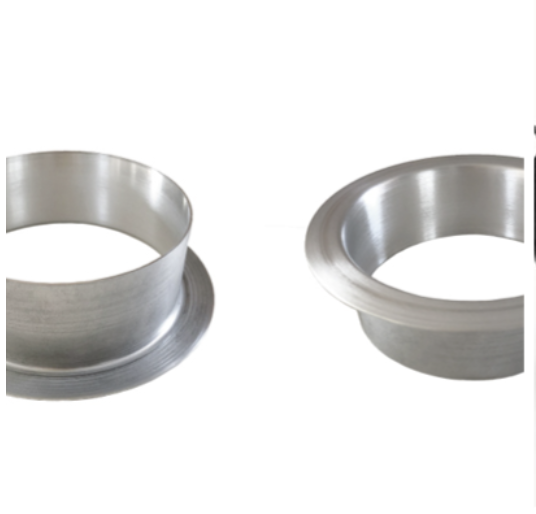
5. Quality Control System Utilizing IT
Since our founding, meeting short lead times and ensuring on-time delivery has been a given. We accommodate customer deadlines, even for complex shapes with deep drawing. By rigorously implementing our self-imposed product inspection standards and establishing these standards at both the inspection and production stages, we achieve a no-claim record.
Thanks to these efforts, our technology has been recognized with awards every year at the “Excellence in Sheet Metal Products Skills Fair (Amada)” and also received the “Tokyo Venture Technology Special Award” in 2016.